Quality assurance – or QA – is more than just checking boxes; it’s about proactively identifying and mitigating risks, optimizing operations, and safeguarding your company’s bottom line. Operational mistakes can lead to delays, damaged goods, unhappy customers, and a tarnished reputation – all of which can significantly impact a company financially.
Let’s navigate the complexities of QA and explore how expert quality assurance can streamline your operations, minimize costs, and fortify your business against risk. We’ll review proven strategies and best practices, providing you with the knowledge and tools to ensure your company thrives.
How Quality Assurance Mitigates Costs and Risks
Quality assurance is a powerful tool for mitigating the costs and risks of logistics. By implementing a robust QA program, businesses can proactively address potential issues, streamline the supply chain, and build a reputation for excellence. Here are some ways that quality assurance can reduce risk and cost for your company:
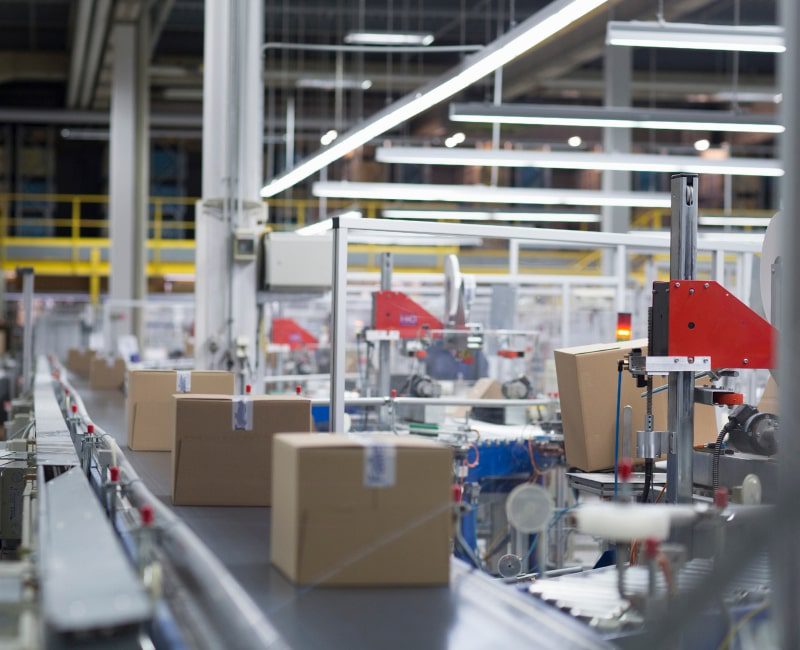
Proactive Problem Prevention
A well-designed QA system actively seeks problems out. By identifying weaknesses in processes before they escalate, companies can avoid costly disruptions, rework, and customer dissatisfaction. Root cause analysis, a key component of quality assurance, dives deeper into the underlying causes of problems, allowing for targeted corrective actions that prevent recurrence. This proactive approach saves resources, reduces downtime, and mitigates risk in the supply chain.
Enhanced Efficiency and Productivity
By streamlining processes, eliminating waste, and standardizing procedures, QA can significantly boost productivity. Well-trained staff, equipped with the knowledge and tools to identify and resolve issues, can contribute to a culture of continuous improvement, where quality is embedded in every aspect of the business. The result is a leaner, more agile organization that can adapt to changing market demands and deliver superior results.
Improved Customer Satisfaction and Loyalty
A strong QA program ensures that products consistently meet or exceed customer expectations, fostering trust and loyalty. A reputation for reliability and quality can be a powerful differentiator, attracting new customers and retaining existing ones. By investing in quality assurance, you’re not just protecting your bottom line; you’re investing in long-term customer relationships that drive sustainable growth.
Regulatory Compliance and Risk Management
For many industries, regulatory compliance is not just a best practice; it’s a legal requirement. Expert quality assurance helps you navigate the complexities of industry standards and regulations, ensuring that your operations are compliant and minimizing the risk of costly penalties or legal action. Moreover, a robust QA system protects your brand’s image by preventing product recalls, safety incidents, and other events that can tarnish your reputation.
Understanding the Cost of Poor Quality (CoPQ)
The Cost of Poor Quality (CoPQ), often hidden beneath the surface of operations, can significantly erode a company’s financial health. Understanding these costs is the first step toward effective quality management.
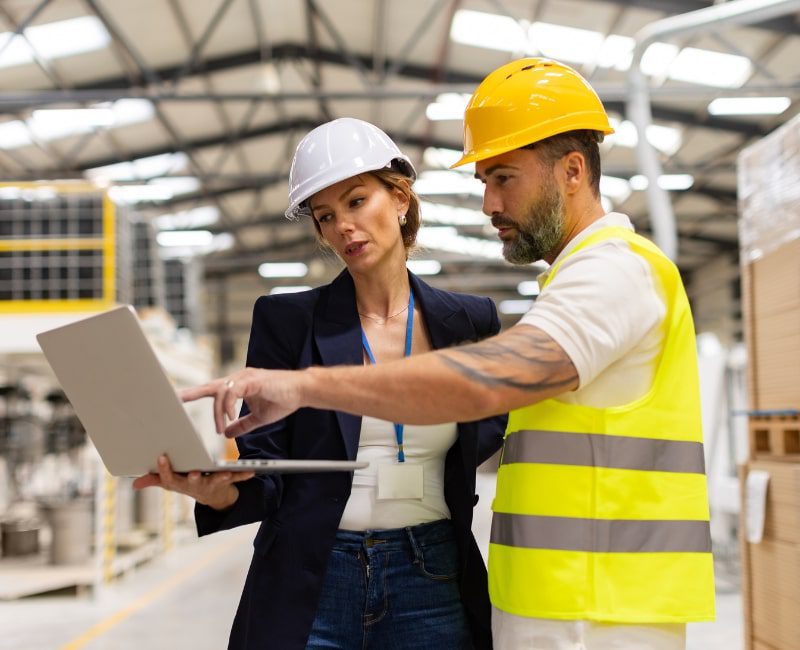
CoPQ encompasses a wide range of expenses, each with an impact on profitability:
Internal Failure Costs: These are the costs incurred before a product reaches the customer. They include the expenses associated with:
- Scrap: Materials and products that cannot be repaired or used and must be discarded.
- Rework: The costs of correcting defects or errors in products or services.
- Process Downtime: The lost productivity and revenue caused by interruptions in the production or delivery process.
External Failure Costs: These costs arise after a product has been delivered to the customer. They include:
- Returns: The costs of processing and replacing returned products.
- Warranty Claims: The expenses incurred to repair or replace products under warranty.
- Loss of Customers: The long-term impact on revenue due to customer dissatisfaction and lost business.
Appraisal Costs: These are the costs associated with evaluating the quality of products or processes. They include:
- Inspections: The costs of examining products to ensure they meet quality standards.
- Testing: The expenses incurred to verify the functionality and performance of products.
- Audits: The costs of assessing the effectiveness of quality management systems.
Prevention Costs: These are investments made to prevent quality problems from occurring in the first place. They include:
- Training: The expenses incurred to educate employees on quality standards and procedures.
- Process Improvement: The costs of analyzing and optimizing processes to enhance quality.
- QA Systems: The investment in technology and infrastructure to support quality assurance efforts.
The CoPQ can quickly escalate, creating a ripple effect throughout your organization. A single defect can trigger a chain reaction, leading to increased internal and external failure costs, higher appraisal costs, and a greater need for prevention measures. This vicious cycle can ultimately drain your resources, hinder growth, and jeopardize long-term success.
The 3PL Approach to Quality Assurance
Partnering with the right third-party logistics (3PL) provider who offers quality assurance services is essential for companies looking to elevate their QA efforts. 3PLs bring a unique blend of expertise, experience, and resources to the table, enabling them to deliver comprehensive and tailored QA solutions that address your specific needs. Here’s what you can expect from a 3PL:
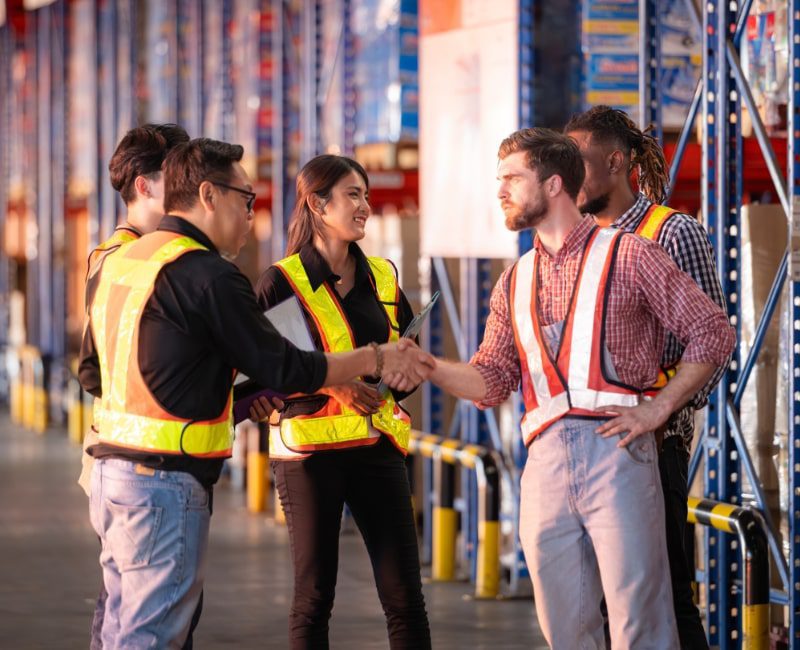
Tailored Solutions
No two businesses are alike, and neither should their QA programs be. The right 3PL will take the time to understand your unique business needs, industry requirements, and operational nuances. They can then leverage this knowledge to develop customized QA programs that align with your goals and objectives, ensuring that your quality assurance efforts are targeted, effective, and relevant to your specific context.
Experienced Professionals
Your 3PL should employ seasoned QA experts with diverse knowledge and experience across various industries. These professionals hold relevant certifications and stay ahead of the latest QA methodologies and best practices through continuous learning and development. Their expertise enables them to identify potential risks, implement effective controls, and drive continuous improvement within your organization.
Proven Methodologies and Tools
Leading 3PLs leverage industry-leading QA practices and cutting-edge technologies to optimize your quality assurance processes. They utilize proven methodologies to streamline operations, reduce waste, and enhance efficiency. Additionally, they employ advanced data analytics tools to gather and analyze critical quality data, providing valuable insights that inform decision-making and drive continuous improvement.
Collaborative Partnerships
3PLs understand that successful quality assurance requires collaboration and partnership. Your partner should work closely with your team, and foster open communication and transparency throughout the QA process. By integrating seamlessly with your existing systems and processes, the right 3PL will ensure a smooth transition and minimal disruption to your operations. A commitment to partnership extends beyond implementation, with ongoing support and guidance to help you achieve your long-term quality goals.
Quality Assurance Solutions for Long-Term Success
When you embrace quality assurance, you gain a competitive advantage that sets you apart in the marketplace. By proactively addressing potential issues before they escalate, optimizing every facet of your operations, consistently exceeding customer expectations, and effectively mitigating risks, expert QA transforms your business from the inside out. It minimizes risk, reduces costs, strengthens your brand’s reputation, and paves the way for sustainable growth.
Are you ready to unlock the full potential of your business through quality assurance solutions? Contact Hanzo Logistics today to discover how our tailored QA solutions can drive sustainable growth for your company. Our team is committed to meeting your unique needs and exceeding your expectations.