Today’s customers expect rapid delivery, which means meeting or beating estimated shipping times is essential for a company’s success. Every minute saved in the warehouse can mean the difference between a satisfied customer and a lost sale. That’s why a streamlined pick-and-pack process is so important in logistical operations. A smooth, efficient fulfillment process directly translates to faster order turnaround, minimized errors, and higher profitability.
By implementing proven strategies and leveraging the right tools, you can transform your pick-and-pack operations and gain a distinct competitive advantage. This comprehensive guide will look into the strategies that can revolutionize your fulfillment center, from optimizing your warehouse layout to implementing cutting-edge technologies.
Laying the Groundwork for Efficient Pick and Pack Operations
By investing time and resources in optimizing your warehouse layout and inventory management, you set the stage for a highly efficient pick-and-pack process. A well-organized warehouse with accurate inventory data minimizes unnecessary movement, reduces errors, and ultimately accelerates your order turnaround time.
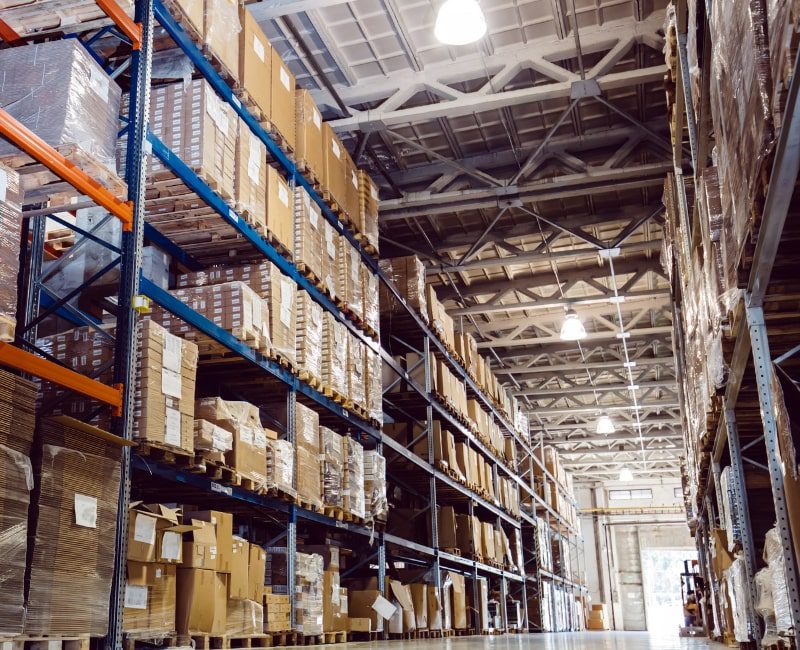
Warehouse Layout Optimization
The physical layout of your warehouse plays a pivotal role in the speed and accuracy of your pick and pack process. Here are three core areas to focus on:
- Strategic Product Placement: Employing ABC analysis, categorize items based on their demand frequency. High-demand (A items) should be located closest to packing stations while slower-moving items (C items) can be stored further away. This minimizes travel time for pickers and maximizes efficiency.
- Efficient Picking Routes: Design picking routes that minimize travel distance and avoid crisscrossing paths. Consider implementing a serpentine or “S-shaped” picking path, where pickers move down one aisle and back up the next.
- Zone Picking Strategies: Divide your warehouse into zones and assign pickers to specific areas. This specialization allows pickers to become familiar with their zone’s layout and product locations, leading to faster and more accurate picks.
Inventory Management Best Practices
Accurate inventory tracking is the backbone of efficient pick-and-pack fulfillment. Knowing precisely what you have on hand, where it’s located, and how much is available enables you to make informed decisions and avoid costly errors. We recommend:
- Accurate Inventory Tracking Systems: Utilize barcode scanning, RFID tags, or other real-time tracking technologies to maintain up-to-the-minute inventory data. This eliminates the need for manual counting and reduces the risk of human error.
- Demand Forecasting and Inventory Replenishment: Analyze historical sales data and seasonal trends to forecast demand accurately. This allows you to proactively replenish inventory, preventing stockouts that can delay order fulfillment.
- Cycle Counting and Inventory Audits: Regularly perform cycle counts, where a small portion of the inventory is counted each day, to verify accuracy. Conduct full inventory audits periodically to reconcile any discrepancies and maintain data integrity.
The Pick and Pack Process
With a well-structured warehouse and accurate inventory data in place, it’s time to focus on the heart of your fulfillment operation: the pick and pack process itself. This is where the right methods and technology can significantly impact your speed and accuracy.
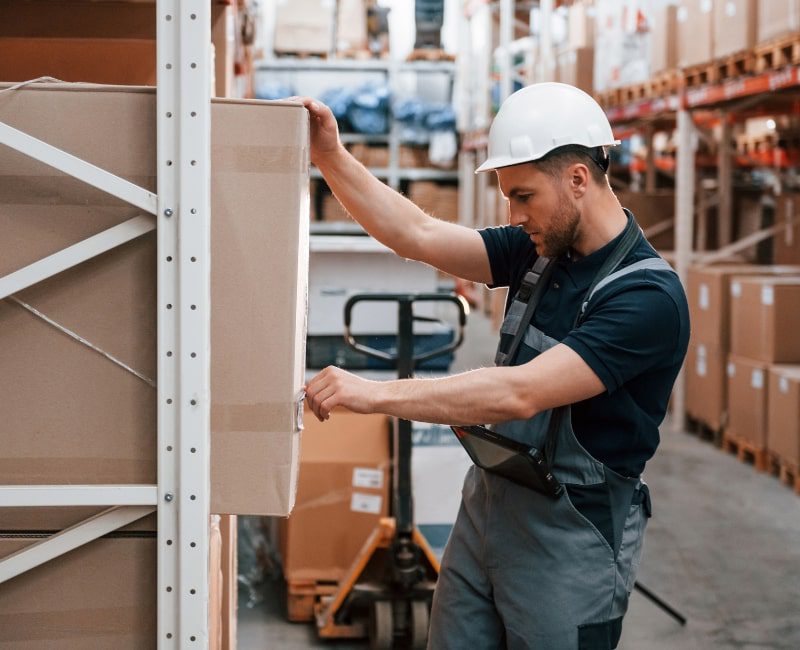
Picking Methodologies
The way you pick items from your warehouse shelves will affect your overall efficiency. Let’s explore some common picking methods:
Piece Picking: Each picker fulfills one order at a time. While simple, it can lead to excessive travel time in large warehouses.
Batch Picking: Pickers gather multiple orders simultaneously. This is most effective when orders contain similar items or are destined for the same shipping area.
Wave Picking: Orders are released in waves throughout the day, allowing for better labor allocation and smoother workflow. This method balances picking efficiency with packing and shipping resources.
Zone Picking: Pickers are assigned to specific zones within the warehouse. This minimizes travel time and allows pickers to develop expertise in their zone’s products.
The optimal picking method for your operation will depend on factors like warehouse size, order volume, and product variety. A 3PL partner can assess your unique needs and recommend the best picking strategy to maximize efficiency and minimize costs.
Technology to Boost Productivity
Technology plays a vital role in modern pick and pack operations, enhancing speed, accuracy, and overall productivity. Here are some key technologies to consider:
Pick-to-Light Systems: LED lights guide pickers to the correct locations and quantities, reducing errors and increasing picking speed.
Voice Picking: Hands-free voice-directed systems allow pickers to receive instructions and confirm picks verbally, improving efficiency and safety.
Mobile Barcode Scanning: Handheld scanners enable quick and accurate item verification and inventory updates.
Warehouse Management Systems (WMS): A WMS serves as the central nervous system of your warehouse, providing real-time inventory visibility, optimizing picking routes, and generating valuable data insights.
The “Pack Out” Process
Efficient packing is the final step in ensuring your orders are shipped quickly, accurately, and securely. Consider these key elements:
Choosing the Right Packaging Materials: Select materials that protect your products during shipping while also being mindful of sustainability. Consider eco-friendly options like recycled cardboard and biodegradable packing peanuts.
Streamlining Packing Stations: Design packing stations with ergonomics in mind, providing ample workspace and easy access to materials.
Quality Control Checks: Implement a thorough quality control process to verify order accuracy before sealing and shipping packages. This final check can prevent costly errors and returns.
By carefully evaluating picking methodologies, investing in productivity-enhancing technologies, and refining your pack-out process, you can create fulfillment operations that are both streamlined and scalable.
Pick and Pack Strategies for Continuous Improvement
To stay ahead of the curve, your company must embrace a culture of continuous improvement. Here are some key strategies to ensure your pick-and-pack fulfillment process remains agile, efficient, and adaptable:
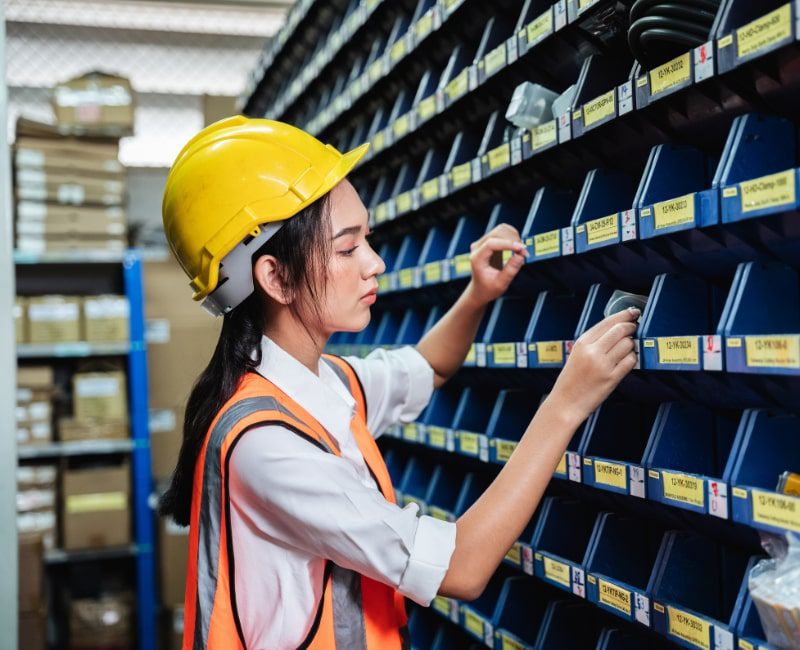
Leveraging Data Analytics
Your warehouse generates a wealth of data that can be harnessed to identify inefficiencies and drive optimization. Track key metrics like order cycle time, picking accuracy, and labor costs. Use data analytics tools to pinpoint bottlenecks in your workflow and areas where automation might be beneficial. Regular data analysis empowers you to make informed decisions based on real-world performance.
Employee Training
Your employees are the heart of your pick-and-pack operation. Invest in comprehensive training programs to ensure they have the skills and knowledge to perform their tasks efficiently and accurately. Recognize and reward high performers to boost morale and foster a culture of excellence. A motivated and well-trained workforce is a key asset in any fulfillment center.
Automation and Robotics
While automation might seem like a significant investment, it can yield substantial returns in the long run. Consider incorporating technologies like automated guided vehicles (AGVs) to transport items, robotic pickers for repetitive tasks, and automated sorting systems to streamline the packing process. Automation can reduce labor costs, improve accuracy, and increase throughput, especially in high-volume operations.
The Value of Lean Principles
The Lean methodology, with its focus on waste reduction and continuous improvement, can revolutionize your pick-and-pack process. Identify and eliminate non-value-added activities like excess movement, waiting time, and overprocessing. Encourage employees to suggest improvements and empower them to implement solutions. Lean principles create a culture of problem-solving and continuous optimization, ensuring your operation remains efficient and adaptable.
By implementing these strategies for continuous improvement, you can transform your pick-and-pack fulfillment operation into a well-oiled machine that consistently exceeds customer expectations. Optimization is not a one-time event; it’s an ongoing commitment to excellence.
3PL Partnerships for Pick and Pack Optimization
While optimizing your pick-and-pack process in-house is certainly achievable, many businesses find that partnering with a third-party logistics (3PL) provider offers a strategic advantage. 3PLs specialize in fulfillment services, bringing a wealth of expertise, technology, and resources to the table.
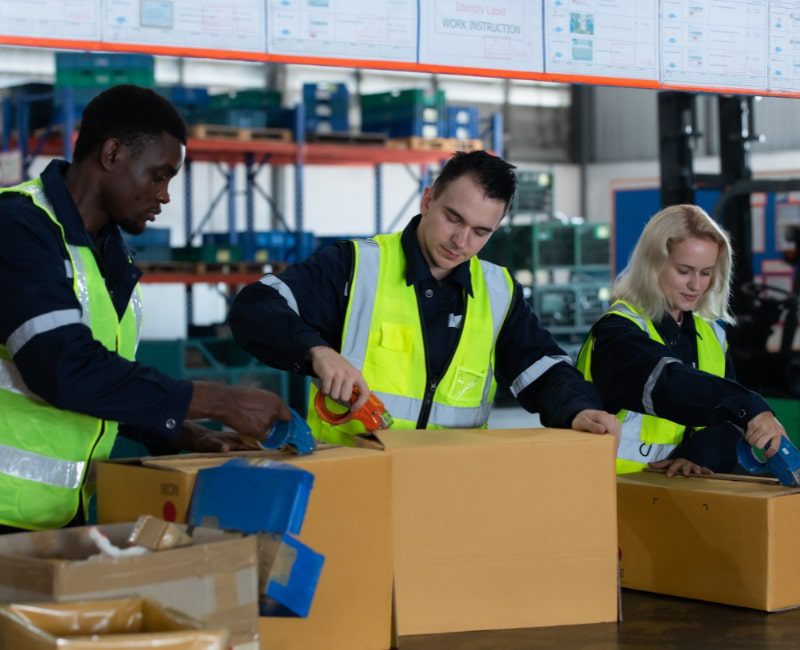
By outsourcing your pick and pack operations to a 3PL, you gain access to a team of logistics professionals who are dedicated to optimizing your fulfillment process. They bring experience and best practices that can significantly accelerate your order turnaround time.
Expertise and Scalability on Demand
3PLs offer a scalable solution, allowing you to adapt to fluctuations in order volume without the need to invest in additional staff or infrastructure. Whether you experience seasonal spikes or steady growth, a 3PL can flex its resources to meet your demands.
Tailored Solutions for Your Unique Needs
No two businesses are alike, and a reputable 3PL will work closely with you to understand your specific requirements. They can customize their services to align with your product types, order volume, and shipping destinations, ensuring a tailored solution that maximizes efficiency.
Data-Driven Insights for Continuous Improvement
3PLs have sophisticated warehouse management systems (WMS) and data analytics tools that provide valuable insights into your operation. These insights can help you identify areas for improvement, track key performance indicators (KPIs), and make data-driven decisions to optimize your pick-and-pack process continuously.
Cost Savings and Risk Mitigation
By leveraging a 3PL’s expertise, technology, and economies of scale, you can achieve significant cost savings in your fulfillment operations. Additionally, 3PLs assume responsibility for many of the risks associated with warehousing and fulfillment, such as inventory management, labor shortages, and facility maintenance.
Partnering with a 3PL can be a game-changer for businesses looking to optimize their pick-and-pack process and achieve faster order turnaround times. By tapping into the expertise and resources of a logistics specialist, you can focus on your core competencies while leaving the complexities of fulfillment to the experts.
Your Path to Pick and Pack Excellence Starts Here
By embracing the strategies outlined in this article, investing in the right technologies, and fostering a culture of continuous improvement, you can transform your fulfillment operation to consistently exceed customer expectations and streamline order turnaround.
Take the first step toward optimizing your pick-and-pack process today. Contact Hanzo Logistics and discover how we can help you simplify your operations and drive sustainable growth. We understand that every business is unique, and we’re committed to providing tailored solutions that address your specific challenges and goals.