At the heart of eCommerce success lies the ability to swiftly and accurately process customer orders. Pick-and-pack fulfillment is the linchpin in this process, encompassing the careful orchestration of selecting products and preparing them for shipping. As consumers increasingly demand quicker deliveries and impeccable service, mastering the art of pick-and-pack fulfillment becomes a strategic imperative for companies navigating the e-commerce landscape.
In this article, we’re delving into pick-and-pack fulfillment, exploring its definition, key components, and the instrumental role it plays in order processing. As businesses worldwide aim to optimize their logistics chains, understanding the workings of pick-and-pack fulfillment becomes a foundational step toward enhancing efficiency, minimizing errors, and ultimately ensuring a seamless customer experience.
Understanding Pick and Pack Fulfillment
Pick-and-pack fulfillment is an order processing method specifically designed to enhance the efficiency of fulfilling customer orders in the eCommerce sector. At its core, it involves the systematic selection (picking) of items from a warehouse inventory and their careful packaging (packing) for shipping. This process is carefully orchestrated to minimize errors, expedite order fulfillment, and optimize the overall supply chain.
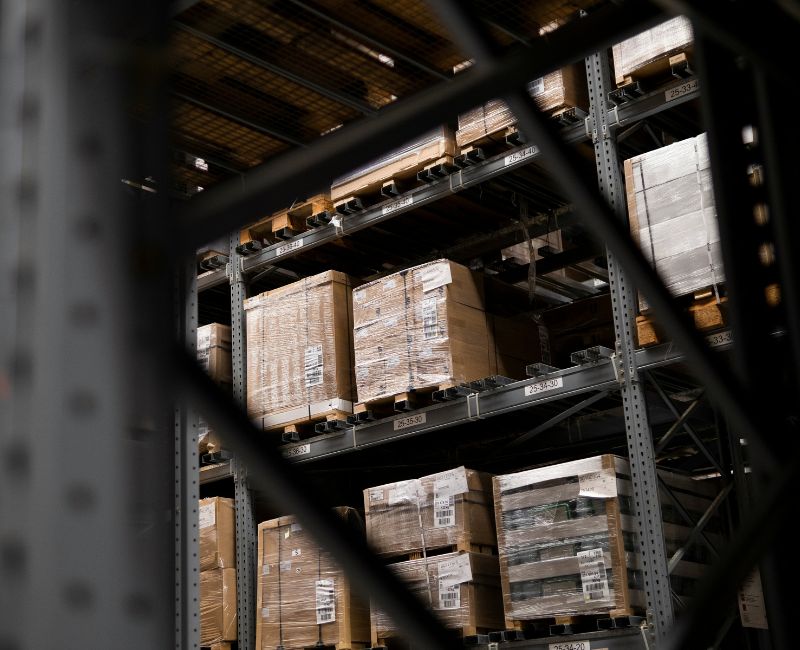
Key Components
Several key components ensure the seamless execution of this order-processing workflow. These components include inventory management systems, picking strategies, packing stations, and quality control measures. The synchronization of these elements is crucial to achieving the overarching goals of accuracy, speed, and cost-effectiveness in meeting customer demands.
Seamless Order Fulfillment
Pick-and-pack fulfillment plays a pivotal role in ensuring the seamless fulfillment of customer orders. By employing this efficient process, businesses can significantly reduce the time it takes to move from order placement to shipment, thereby enhancing the overall customer experience. The precision and reliability inherent in the pick-and-pack method contribute to the timely delivery of products.
Impact on Customer Satisfaction
The impact of pick-and-pack fulfillment extends beyond mere operational efficiency—it directly influences customer satisfaction. Timely and accurate order fulfillment contributes to a positive customer experience, fostering trust and loyalty. In an era where customer expectations are continually on the rise, businesses that excel in efficient fulfillment gain a competitive edge by meeting and exceeding these expectations, resulting in satisfied and repeat customers.
Efficiency and Cost-effectiveness
Beyond customer satisfaction, pick-and-pack fulfillment holds the key to cost-effectiveness. Streamlining the order-processing workflow minimizes errors, reduces unnecessary labor, and optimizes resource utilization. This not only enhances the speed of order fulfillment but also contributes to cost savings, allowing businesses to allocate resources more effectively and invest in further improving their services.
The Pick and Pack Process
The pick-and-pack journey begins with the reception of customer orders – and the process of order verification and inventory checks. Warehouse personnel ensure that the ordered items are in stock and ready for picking. Modern systems are adept at real-time inventory management, reducing the likelihood of errors and ensuring that customers only order physically available items.
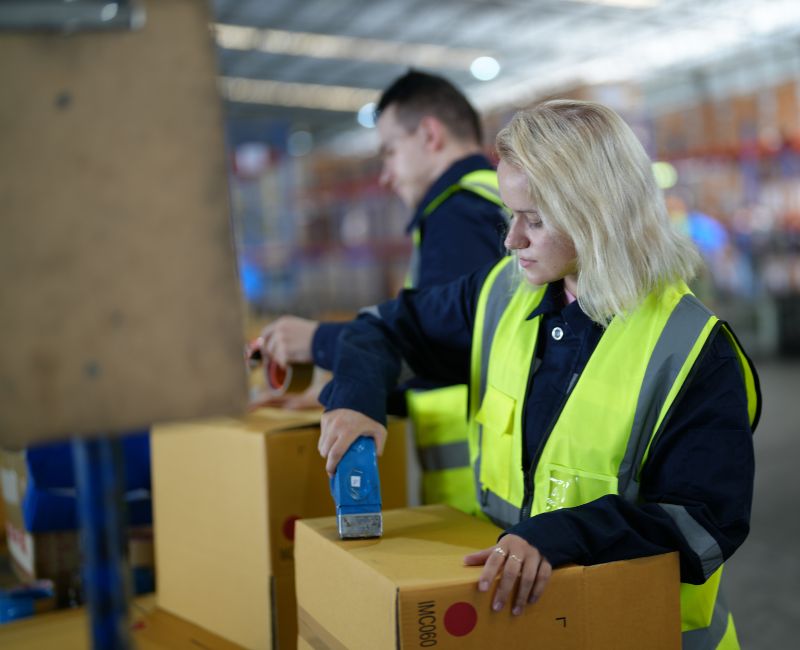
Order Picking: Once the inventory is confirmed, the picking phase commences. This step involves retrieving items from their designated storage locations within the warehouse. Optimization of picking routes, whether manual or automated, is crucial in minimizing the time and resources required to gather all the items for a specific order.
Packing and Labeling: With the items collected, the focus shifts to the packing and labeling of the order. Packaging materials are selected based on the nature of the products to ensure they reach their destination in pristine condition. Additionally, each package is accurately labeled, providing essential information for both logistics and customers, including shipping addresses, order details, and any necessary product information.
Shipping and Tracking: The final leg of the pick-and-pack process involves the actual shipping of packages to their destinations. This step is not merely about sending off the order but includes integrating tracking mechanisms. Customers are provided with real-time visibility into the shipping progress, enhancing the overall experience and allowing for proactive communication regarding delivery times.
Automation in Pick and Pack
Modern warehouses leverage automation technologies to enhance the efficiency of the pick-and-pack process. Automated guided vehicles (AGVs) and robotic systems assist in the movement of goods, reducing the reliance on manual labor and expediting the picking and packing stages. Automation ensures a faster turnaround time, especially in high-volume order scenarios.
Use of Warehouse Management Systems (WMS)
Warehouse Management Systems (WMS) act as the digital backbone of pick-and-pack fulfillment. These systems optimize inventory management, order processing, and logistics coordination. WMS facilitates real-time data exchange, enabling warehouse operators to make informed decisions and respond rapidly to changes in demand or inventory levels.
Barcode Scanning and RFID Technology
Barcode scanning and Radio-Frequency Identification (RFID) technology play pivotal roles in ensuring accuracy throughout the pick-and-pack process. Barcode scanners streamline order picking by minimizing errors, while RFID technology offers real-time tracking and visibility into the movement of products within the warehouse. These technologies collectively contribute to precision, efficiency, and improved overall reliability in pick-and-pack fulfillment.
Benefits of Pick and Pack Fulfillment
The multifaceted advantages that businesses can derive from a robust pick-and-pack process range from heightened accuracy to increased efficiency and the ability to adapt seamlessly to varying demands.
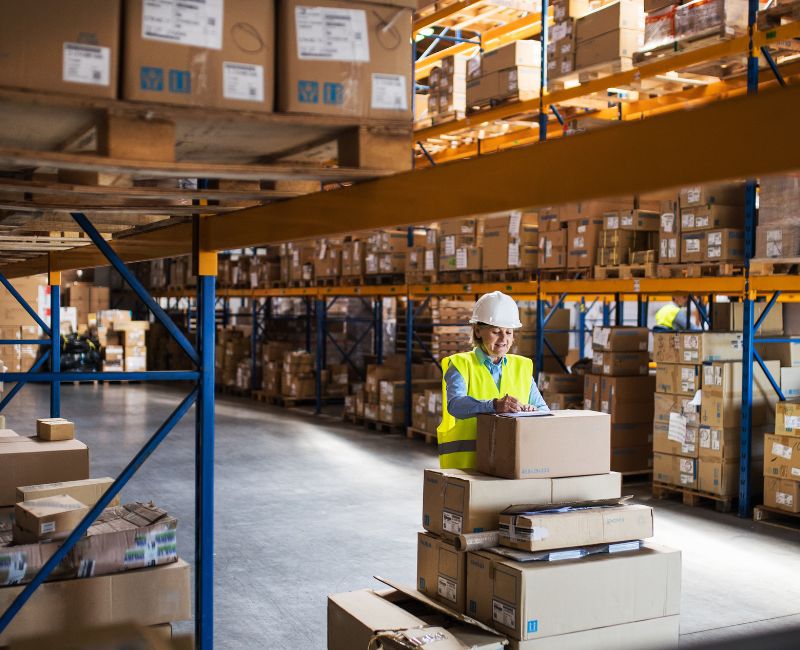
Improved Accuracy
Reducing Order Errors: One of the primary benefits of pick-and-pack fulfillment lies in its ability to significantly reduce order errors. The meticulous nature of the process, coupled with technology integration, minimizes the chances of picking the wrong items or packaging errors. This heightened accuracy not only enhances customer satisfaction but also contributes to a reduction in costly returns and associated operational challenges.
Minimizing Returns: The precision embedded in the pick-and-pack process translates into a notable reduction in product returns. By ensuring that customers receive the correct items in optimal condition, businesses can mitigate the costs and complexities associated with the return process. This not only enhances the overall operational efficiency but also fosters customer trust and loyalty.
Enhanced Efficiency
Streamlining Operations: Pick-and-pack fulfillment streamlines overall warehouse operations. The systematic approach to order processing, coupled with technology-driven automation, eliminates bottlenecks and reduces the time and resources required for each order. This operational streamlining not only improves the internal workflow but also enables businesses to handle a higher volume of orders without compromising accuracy or efficiency.
Faster Order Processing Times: The efficiency gains realized through pick-and-pack fulfillment directly translate into faster order processing times. Swift and accurate order fulfillment is a key driver of customer satisfaction, especially in an era where quick deliveries are the norm. Businesses that excel in reducing the time it takes from order placement to shipping gain a competitive advantage, meeting and often exceeding customer expectations.
Scalability and Flexibility
Adapting to Business Growth: Pick-and-pack fulfillment is designed to be scalable, making it an invaluable asset for businesses experiencing growth. The modular nature of the process allows for seamless integration of additional resources and technology to accommodate increased order volumes. This scalability ensures that businesses can adapt to changing demands without compromising on accuracy or efficiency.
Handling Seasonal Demand: Seasonal fluctuations in demand are a common challenge for eCommerce businesses. The flexibility inherent in pick-and-pack fulfillment allows organizations to efficiently handle spikes in demand during peak seasons. Whether it’s a holiday rush or a special promotional event, businesses can navigate varying order volumes with agility, ensuring that customer expectations are consistently met.
Best Practices in Pick and Pack Fulfillment
According to a research report by Modern Materials Handling, 45% of companies face issues with order picking and processing. This is why adopting best practices in this type of fulfillment is essential. The key strategies that organizations can implement to elevate their pick-and-pack fulfillment operations focus on organizational strategies and the critical aspects of communication and collaboration.
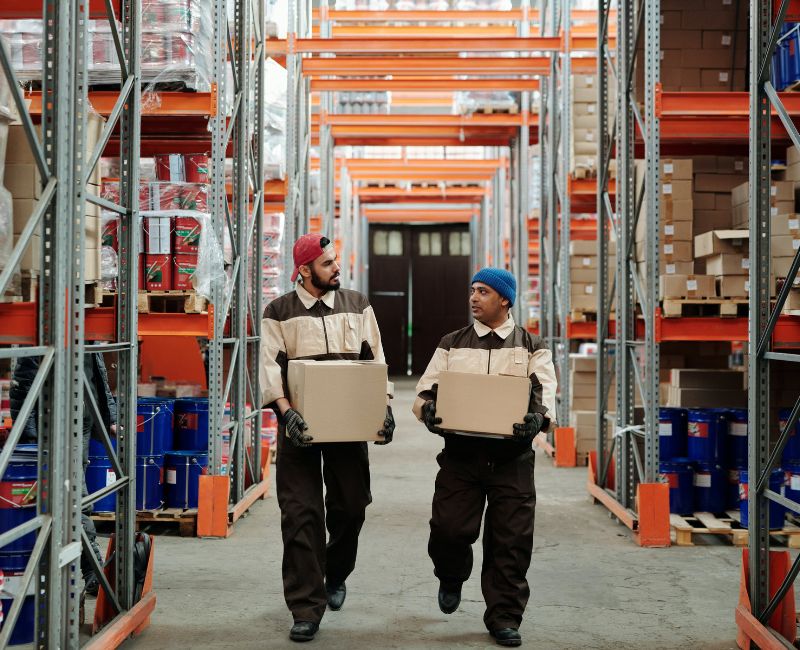
Organizational Strategies
Efficient Warehouse Layouts: Efficient warehouse layouts are foundational to the success of pick-and-pack fulfillment. Strategic organization of storage areas, picking zones, and packing stations minimizes travel time, reduces errors, and enhances overall operational efficiency. By implementing a layout that aligns with the order processing workflow, businesses can streamline the movement of products from inventory shelves to shipping carriers.
Regular Audits and Quality Control: Regular audits and quality control measures are essential components of a successful pick-and-pack strategy. Implementing routine checks on inventory accuracy, order picking accuracy, and packaging quality helps identify and rectify potential issues before they impact customer satisfaction. This proactive approach not only maintains the integrity of the process but also contributes to ongoing process improvement.
Communication and Collaboration
Coordination Between Departments: Seamless coordination between various departments within an organization is vital for effective pick-and-pack fulfillment. Close collaboration between the sales, marketing, and warehouse teams ensures that accurate and up-to-date product information is available. Timely communication about promotions, product launches, or changes in demand enables the warehouse to adjust its operations accordingly, reducing the risk of errors and delays.
Integration with Suppliers and Partners: The integration of pick-and-pack operations with suppliers and partners is a strategic move that enhances overall supply chain efficiency. Establishing clear communication channels and shared data interfaces with suppliers ensures that the warehouse is well-informed about incoming inventory and potential disruptions. Collaborative efforts with logistics partners facilitate a smooth transition from warehouse to transportation, minimizing handling times and improving order delivery speed.
The Strategic Impact of Pick and Pack Fulfillment
The role of the pick-and-pack method in facilitating seamless order fulfillment, minimizing errors, and optimizing operational efficiency cannot be overstated. Businesses that adopt pick-and-pack fulfillment position themselves as leaders in the race to deliver exceptional customer experiences.
At Hanzo, we believe that by embracing the best practices and leveraging the benefits this process offers, your business can build a robust foundation for sustained success in the competitive world of online retail. We redefine retail and eCommerce logistics services by prioritizing precision, efficiency, and adaptability.
As technology continues to advance, and consumer expectations evolve, the importance of an efficient and adaptable pick-and-pack process becomes even more pronounced. The ability to integrate organizational strategies, maintain clear communication channels, and continually refine operations through audits and quality control measures ensures that pick-and-pack fulfillment remains not just a process but a strategic advantage.