In its most basic form, supply chain management is the planning and execution of all activities involved in getting a product from its raw materials to the end consumer. Reverse logistics, an essential part of supply chain management, deals with the movement of goods in the reverse direction, from the customer back to the retailer or manufacturer.
From processing returned items and managing product recalls to responsibly handling end-of-life products, reverse logistics can encompass a variety of scenarios. And as the importance of sustainability and customer satisfaction grows, so too does the significance of efficient reverse logistics practices.
Let’s explore reverse logistics, its various components, and its growing role in the modern supply chain. We’ll also show you how third-party logistics providers, or 3PLs, can be your secret weapon for streamlining these crucial processes.
Understanding Reverse Logistics
In essence, reverse logistics is the process of managing the efficient return, reuse, or disposal of goods that are moving back up the supply chain. This encompasses a wide range of activities, from processing customer returns to coordinating product recalls and even managing the lifecycle of used or unwanted items.
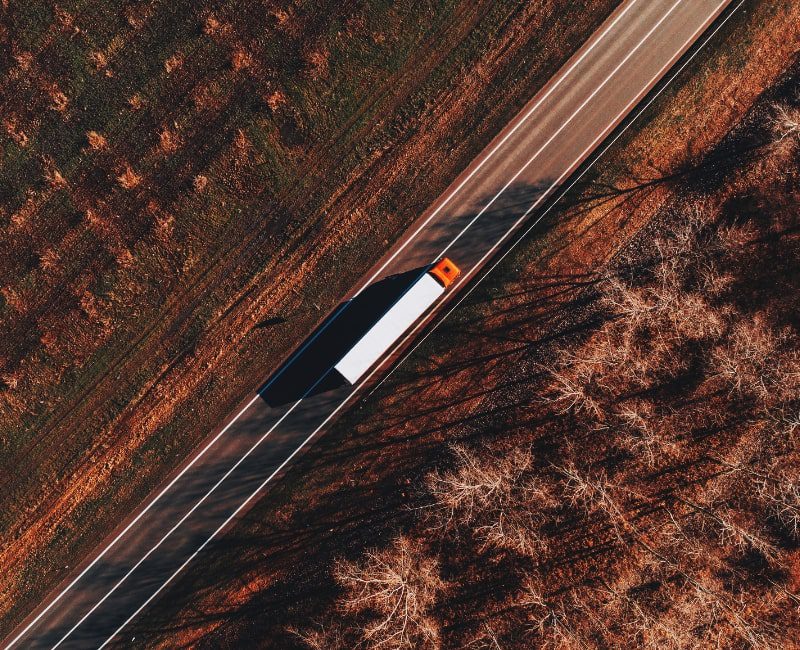
Key Drivers of Reverse Logistics
Understanding the key drivers of reverse logistics is crucial for crafting an effective strategy. Here are some of the most common reasons products might flow back through the supply chain:
Customer Returns: Not every purchase goes according to plan. Damaged products, incorrect items, or simply a change of heart can lead to customer returns. Reverse logistics ensures these returns are processed efficiently, minimizing disruption and keeping customers satisfied.
End-of-Life Products & Recalls: Every product eventually reaches the end of its usable life. Reverse logistics plays a vital role in responsibly managing these end-of-life products, whether through proper disposal or exploring opportunities for recycling or refurbishment. Additionally, in the case of product recalls, reverse logistics ensures a safe and efficient collection of potentially faulty items.
Refurbishment & Remanufacturing Opportunities: Not all returned products are destined for the scrap heap. Reverse logistics can identify items that can be refurbished or remanufactured, giving them a second life and extending their overall value. This not only reduces waste but can also create new revenue streams.
Inventory Management & Seasonal Products: Even the most meticulous forecasting can lead to excess inventory. Reverse logistics helps manage these situations by facilitating the return or redistribution of unwanted stock, ensuring efficient inventory control, especially for seasonal products with fluctuating demand.
The Role of 3PLs in Reverse Logistics
Navigating the complexities of reverse logistics can be daunting. This is where Third-Party Logistics providers, or 3PLs, step in as your strategic partners. By leveraging their expertise and infrastructure, 3PLs can significantly enhance your reverse logistics strategy, streamlining processes and maximizing efficiency.
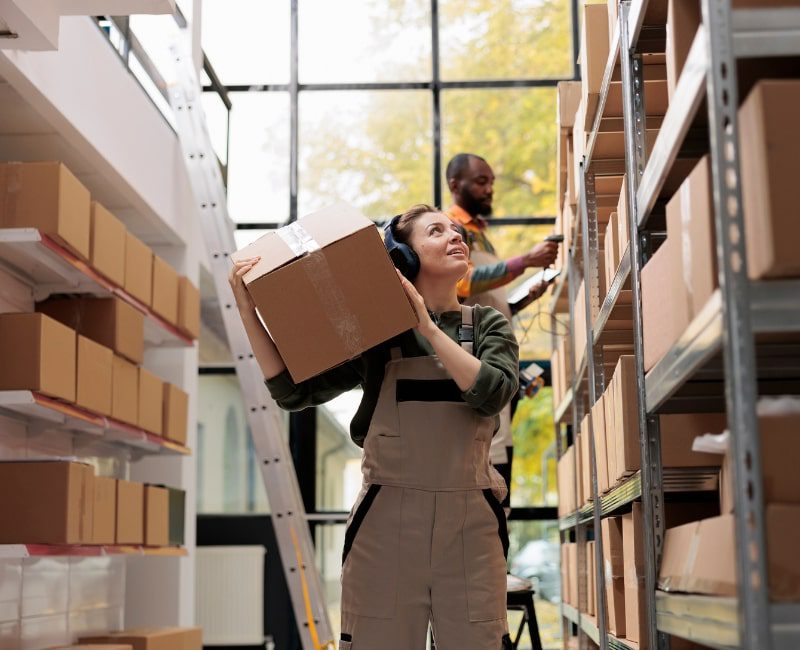
Here’s how a 3PL can help your business create and manage a robust reverse supply chain:
Returns Management & Processing: 3PLs can handle the entire returns process, from generating return labels and managing Return Merchandise Authorization (RMA) to efficiently receiving and processing returned goods. This frees up your resources to focus on core business activities.
Warehousing & Inventory Control for Returned Goods: 3PLs offer dedicated warehousing space for managing returned items. This ensures proper organization and control of your reverse inventory, minimizing the risk of damage or loss.
Product Inspection & Disposition (Restock, Refurbish, Recycle, Dispose): 3PLs can meticulously inspect returned products, determining each item’s optimal course of action. This could involve restocking sellable goods, identifying opportunities for refurbishment, or responsibly recycling or disposing of unusable items.
Value Recovery & Asset Management: Some 3PLs go beyond simply processing returns. They can help you identify opportunities to recover value from returned goods, whether through refurbishment and resale or responsible recycling programs. This not only minimizes waste but can also generate additional revenue.
Repackaging & Re-distribution: For certain products, 3PLs can handle repackaging and redistributing returned items that are still in good condition. This reduces overall waste and maximizes the value you extract from your inventory.
Benefits of Using a 3PL for Reverse Logistics
A seamless and efficient reverse logistics experience can be a major differentiator for your business. Partnering with a 3PL for your reverse logistics needs offers a multitude of benefits, impacting everything from customer satisfaction to your environmental footprint.
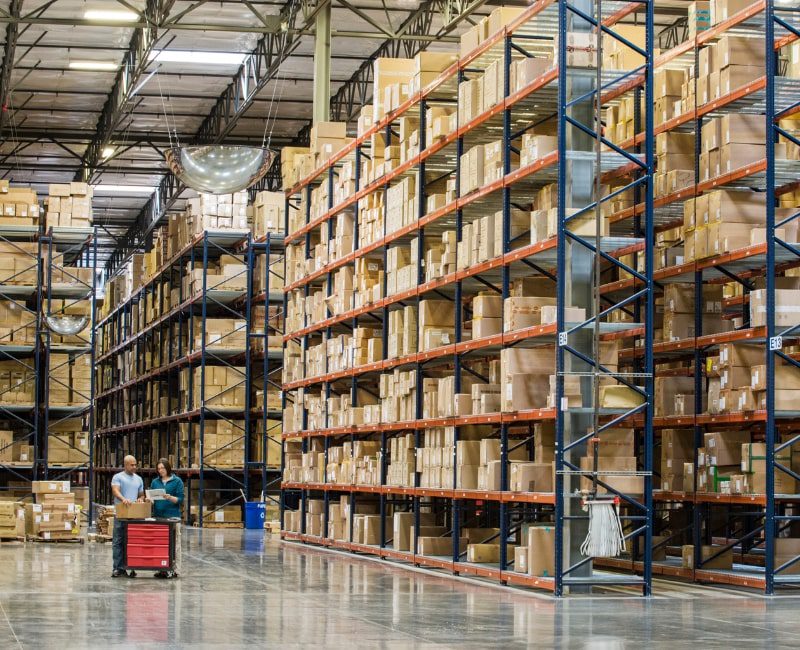
Improved Customer Satisfaction
A smooth returns process is crucial for building customer loyalty. 3PLs handle returns efficiently, minimizing processing times and keeping customers informed throughout the journey. This translates to happier customers, more likely to return for future purchases.
Reduced Processing Times: 3PLs have established systems and expertise to streamline the returns process. This means faster turnaround times for customer refunds or replacements, minimizing frustration and keeping them informed every step of the way.
Simplified Returns Experience: 3PLs can offer user-friendly return portals and generate pre-paid return labels, making returns effortless for your customers. This translates into a more positive brand perception and increased customer loyalty.
Enhanced Communication: 3PLs can provide real-time tracking information and keep customers updated on the status of their return. This transparency fosters trust and builds confidence in your customer service.
Cost Reduction & Increased Efficiency
Reverse logistics can be a hidden cost center. 3PLs bring economies of scale and expertise, optimizing processes and reducing overall costs associated with returns management, warehousing, and product handling. This increases your profit and allows you to allocate resources to core business activities.
Economies of Scale: 3PLs manage reverse logistics for multiple clients, allowing them to negotiate better rates for warehousing, transportation, and waste disposal. These savings are passed on to you, reducing your overall reverse logistics costs.
Optimized Warehousing & Inventory Management: 3PLs have dedicated space and expertise for handling returned goods. This ensures efficient organization and control of your reverse inventory, minimizing storage costs and the risk of damage or loss.
Streamlined Processing: 3PLs utilize advanced technology and established workflows to expedite the processing of returned items. This reduces labor costs associated with in-house returns management, freeing up your resources.
Minimized Waste & Environmental Impact
Responsible disposal and maximizing the life cycle of products are becoming increasingly important. A 3PL can help you implement sustainable practices by identifying opportunities for refurbishment, responsible recycling, and proper disposal of unusable items. This not only reduces your environmental impact but can also enhance your brand image.
Sustainable Practices: 3PLs can help you implement environmentally friendly practices by analyzing returned goods and identifying opportunities for refurbishment or responsible recycling. This reduces the amount of waste going to landfills.
Product Lifecycle Management: 3PLs can help extend the life cycle of your products by managing refurbishment programs and identifying opportunities for parts or materials to be reused. This minimizes your environmental footprint and promotes a more sustainable brand image.
Compliance with Regulations: 3PLs stay up-to-date on ever-evolving environmental regulations regarding product disposal. They ensure proper handling of hazardous materials and responsible recycling practices, minimizing your risk of non-compliance penalties.
Expertise & Scalability
Managing reverse logistics in-house can be challenging, especially during peak seasons or with unexpected surges in returns. 3PLs bring a wealth of experience and established infrastructure to the table. They can handle fluctuating return volumes efficiently, ensuring your reverse supply chain remains adaptable and scalable to meet your evolving needs.
Industry Knowledge & Best Practices: 3PLs possess extensive experience in reverse logistics across various industries. They can leverage this knowledge to develop and implement best practices tailored to your specific needs.
Scalable Infrastructure: 3PLs have the infrastructure and resources to handle fluctuating return volumes, especially during peak seasons. This ensures your reverse supply chain remains adaptable and can easily scale up or down based on your demand.
Dedicated Team & Expertise: A dedicated team of experts at the 3PL will manage your reverse logistics operations. This frees your internal team to focus on core business objectives while ensuring your returns are handled efficiently.
By partnering with a 3PL for your reverse logistics needs, you can reap significant benefits in terms of customer satisfaction, cost reduction, environmental impact, and operational efficiency.
Best Practices in 3PL Reverse Logistics
Building a robust and efficient reverse logistics operation requires a strategic approach. By implementing best practices, you can create a more streamlined and sustainable reverse logistics operation, ultimately enhancing customer satisfaction, increasing profitability, and optimizing your overall supply chain.
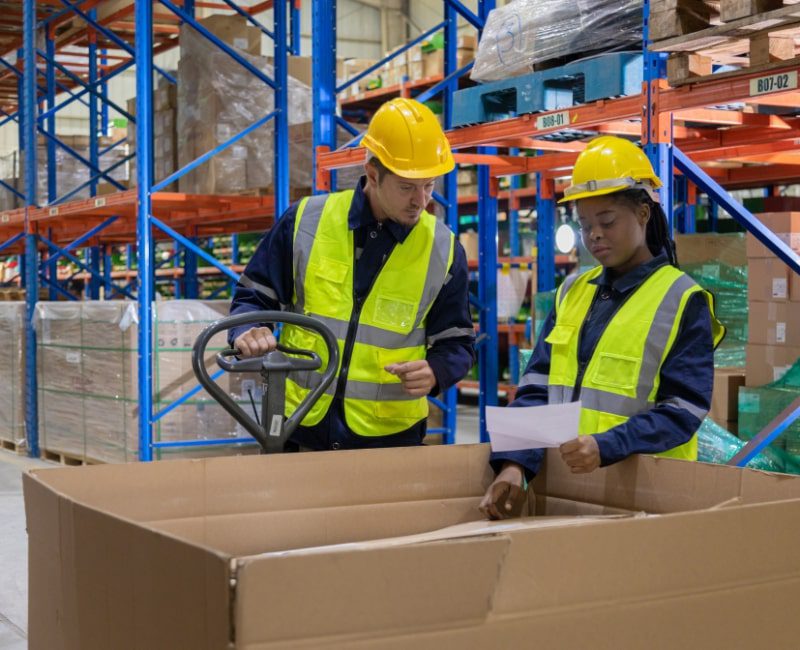
Setting Clear Return Policies
The foundation of a smooth reverse logistics experience lies in establishing transparent and customer-friendly return policies. Communicate your return window and any eligibility requirements upfront. Define different return scenarios, such as defective items, wrong size, or unwanted purchases, and outline the corresponding actions for each. Offering multiple return methods, such as in-store returns, mail returns, or carrier pickups, gives your customers flexibility and convenience.
Streamlining the Returns Process
Customers expect a hassle-free return experience. Implement a user-friendly returns portal on your website for online returns. This portal should be intuitive and guide customers through the return process with ease. Providing pre-paid return labels or offering an easy-to-access return label generation system eliminates a major pain point for customers and expedites the return process. Finally, clearly communicate return processing timelines and keep your customers informed throughout the journey. Sending automated updates on the status of their return fosters trust and transparency.
Efficient Warehousing and Inventory Management
Proper organization and control of your returned goods are crucial for efficient reverse logistics. Designate a dedicated space within your warehouse or utilize your 3PL’s facilities for returned items. This ensures clear separation from new inventory and minimizes the risk of damage or loss. Implement a robust inventory management system to track returned items. This system should allow you to categorize returned goods by reason for return, condition, and restocking potential. Conduct regular audits of your reverse inventory to identify opportunities for consolidating similar items or purging obsolete inventory that cannot be refurbished or resold.
Effective Product Disposition Strategies
Develop clear criteria for determining the optimal course of action for each item. This could involve restocking sellable goods, identifying opportunities for refurbishment or remanufacturing, or responsibly recycling or disposing of unusable items. Partnering with reputable refurbishment or recycling vendors can help you maximize value recovery from returned products. Prioritize environmentally responsible disposal practices whenever possible.
Utilizing Technology and Data Analytics
Technology plays a vital role in optimizing reverse logistics. Leverage technology solutions to automate returns processing tasks like data capture and routing returned items. Analyzing return data allows you to identify trends and patterns. For instance, you might discover that a specific product category has a high return rate due to sizing issues. This valuable insight can then be used to improve product descriptions or sizing charts, ultimately reducing future returns. Return data can also be used to optimize packaging materials and minimize transportation costs associated with returns. By using the right-sized boxes and protective packaging, you can not only reduce costs but also minimize the environmental impact of your reverse logistics operations.
Building Strong Partnerships
A successful reverse logistics strategy relies on strong partnerships. Collaborate with your chosen 3PL to develop and implement efficient reverse logistics processes. Their expertise and established infrastructure can significantly enhance your capabilities. Maintain clear communication channels with all partners involved in the reverse supply chain, including carriers, refurbishing vendors, and recycling facilities. Regularly evaluate and update your partnerships to ensure everyone is aligned with your goals and that your reverse logistics operations are functioning at peak efficiency.
The Power of Partnership: Optimizing Your Reverse Logistics
As customer expectations for seamless returns and environmental responsibility continue to rise, companies must prioritize the efficiency and sustainability of their reverse supply chains. With the growing importance of reverse logistics, partnering with a 3PL provider can be your game-changer for streamlined returns processing and minimized costs. The right 3PL partner will empower you to build a robust and environmentally responsible reverse supply chain.
Ready to unlock the power of efficient reverse logistics for your business? At Hanzo Logistics, our expert team possesses the experience and infrastructure to design and implement customized logistics solutions that meet your unique needs. Contact us today to discuss how we can transform your reverse supply chain and help you achieve greater operational efficiency in your business.