At the heart of logistics precision lies quality assurance (QA), a fundamental practice that ensures the seamless flow of high-quality products and services. QA serves as the bedrock for ensuring that every link in the supply chain functions seamlessly, from warehousing and transportation to distribution. It minimizes the risk of disruptions, enhances operational efficiency, and elevates customer satisfaction. As businesses increasingly rely on third-party logistics providers, the integration of robust quality assurance processes becomes a strategic imperative.
By exploring the foundations, benefits, and real-world applications of QA, we want to explain why a steadfast commitment to quality is not merely a choice but a cornerstone for businesses seeking 3PL partners. Through this exploration, we’ll equip businesses with insights that empower them to make informed decisions and forge partnerships that align seamlessly with their commitment to delivering excellence in their respective industries.
The Foundations of Quality Assurance
In the realm of logistics, quality extends beyond the end product; it encompasses the entire process from origin to destination. Quality in logistics is the assurance that every link in the supply chain functions cohesively, meeting predetermined standards and specifications. This includes the accuracy of inventory management, timely delivery, and the integrity of products during transportation. Defining and upholding these benchmarks ensures a seamless and reliable flow of goods, bolstering the overall efficiency of the logistics network.
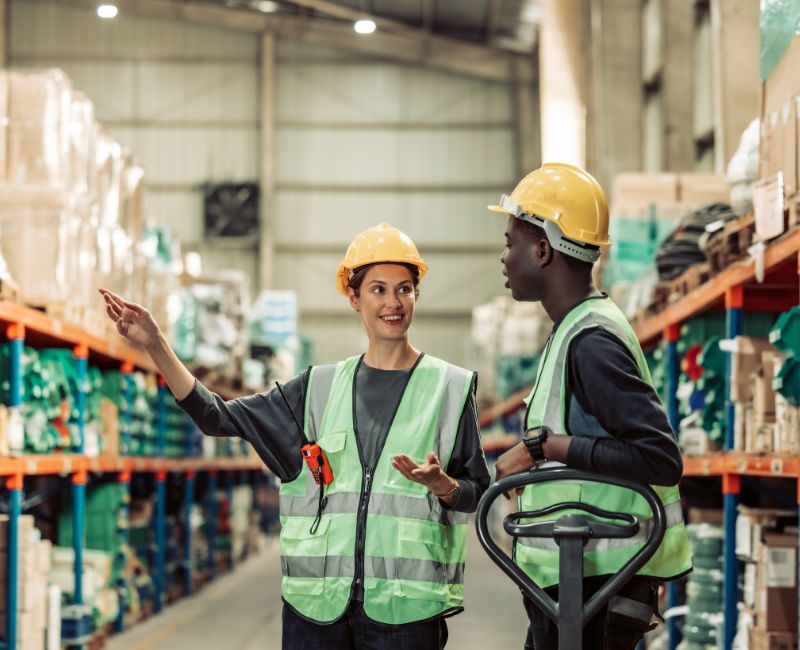
The Role of Standard Operating Procedures (SOPs)
Central to the application of quality assurance in logistics is the establishment and adherence to Standard Operating Procedures (SOPs). SOPs serve as the blueprint for operational excellence, providing a systematic guide for each stage of the logistics process. From inventory handling to transportation protocols, SOPs set the standard for consistency and best practices. By meticulously following these procedures, 3PLs ensures that each facet of the supply chain is executed with precision, minimizing variability and enhancing overall quality.
Regulatory Compliance in Logistics
The intricacies of global logistics necessitate compliance with a myriad of regulations and standards. Regulatory Compliance in logistics ensures adherence to local and international laws governing the transportation, handling, and delivery of goods. From customs regulations to safety standards, compliance not only mitigates legal risks but also reinforces the commitment to delivering products and services of the highest quality. Your 3PL partner should consistently align operations with the latest regulatory requirements to guarantee the integrity of your supply chain.
Benefits of Quality Assurance in Logistics
From enhancing customer satisfaction through meeting and exceeding expectations to mitigating risks and fortifying operational efficiency, the multifaceted advantages of QA serve as a linchpin for ensuring the seamless flow of high-quality products and services.
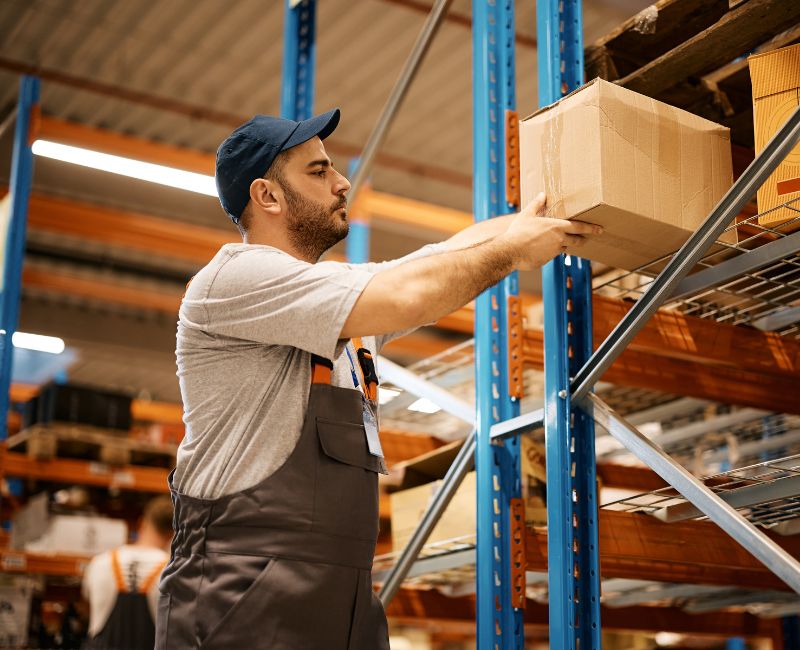
Enhanced Customer Satisfaction
Meeting Client Expectations: Quality assurance in logistics serves as the foundation for meeting and exceeding client expectations. By ensuring that products arrive on time, undamaged, and in accordance with specifications, QA instills confidence in clients and fosters long-term partnerships.
Building Trust and Credibility: Reliability is the cornerstone of trust in logistics. Through a rigorous commitment to quality assurance, 3PLs build trust with clients, establishing credibility in the industry. This trust is not just a transactional benefit but a strategic asset in maintaining enduring client relationships.
Risk Mitigation
Identifying and Minimizing Risks: Quality assurance is a proactive approach to risk management. By systematically identifying potential risks within the supply chain, your 3PL provider should implement preemptive measures to minimize disruptions, ensuring the continuity and reliability of logistics operations.
Ensuring Compliance with Industry Standards: Compliance with industry standards is not just a regulatory requirement but a critical aspect of risk mitigation. Quality assurance goes beyond meeting minimum standards; it involves a commitment to exceeding these benchmarks and fortifying the supply chain against unforeseen challenges.
Operational Efficiency
Streamlining Processes: Quality assurance optimizes logistics processes by streamlining workflows and eliminating inefficiencies. Through continuous evaluation and improvement, QA enhances operational efficiency, reducing lead times and enhancing the overall agility of the supply chain.
Reducing Errors and Rework: Errors in logistics operations can have cascading effects. Quality assurance focuses on error prevention, minimizing the need for rework. By implementing robust processes and checks, the company reduces errors, ensuring that each step of the logistics process contributes to the delivery of high-quality services.
Choosing a 3PL Partner with a Focus on Quality Assurance
As businesses navigate the complex terrain of logistics, the selection of a third-party logistics (3PL) partner becomes a strategic decision that significantly influences supply chain performance. A critical factor in this decision-making process is the emphasis placed on Quality Assurance (QA) by prospective partners.
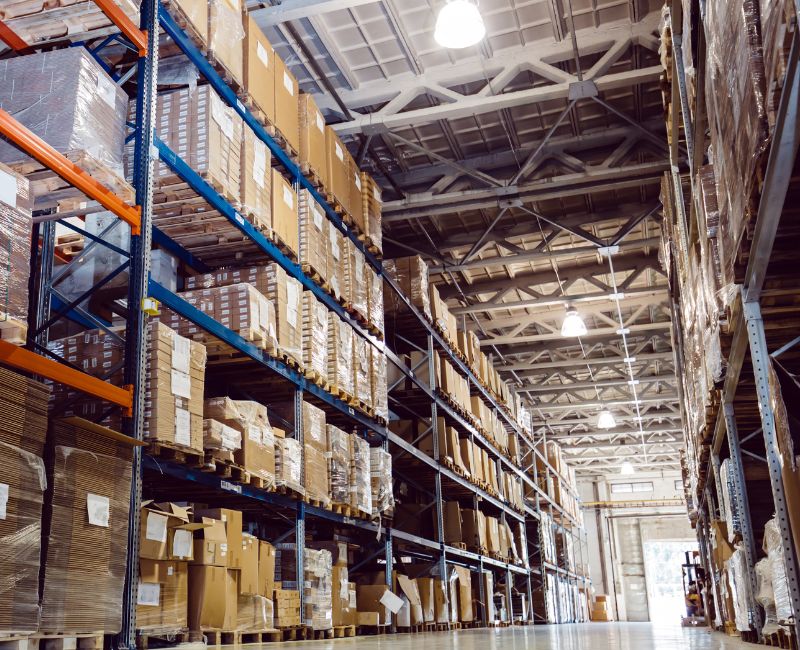
Evaluating a 3PL’s QA Processes
Before entrusting your supply chain to a 3PL partner, a thorough evaluation of their QA processes is imperative. Look beyond surface-level assurances and delve into the intricacies of their quality control measures. Consider how the 3PL identifies, assesses, and rectifies deviations from established standards. At Hanzo Logistics, our commitment to QA is underlined by transparent processes that span from initial product receipt to final delivery, ensuring the highest quality at every stage.
Questions to Ask When Selecting a 3PL Partner
When selecting a third-party logistics partner, posing insightful questions is instrumental in ensuring the alignment of their practices with your business goals.
- How is quality monitored throughout the supply chain?
Assess the comprehensiveness of their quality monitoring, from warehouse operations to transportation logistics. Understanding the depth and breadth of a 3PL’s quality monitoring mechanisms provides insights into their commitment to maintaining high standards. Inquire about the specific tools, technologies, and methodologies employed at various stages of the supply chain. A robust QA framework should encompass not only product quality but also the reliability of processes, accuracy in inventory management, and adherence to timelines.
- What measures are in place for risk mitigation?
Inquire about their strategies for identifying and mitigating potential risks to ensure the resilience of your supply chain. Risk mitigation is essential to effective logistics management. Delve into the 3PL’s approach to risk identification, assessment, and mitigation. This should include considerations for external factors such as geopolitical events, natural disasters, and supply chain disruptions. A comprehensive risk mitigation strategy ensures that your supply chain remains robust and adaptable in the face of unforeseen challenges.
- How does the 3PL handle non-compliance with industry standards?
Understanding how deviations from standards are addressed is crucial for maintaining the integrity of your operations. Compliance with industry standards is non-negotiable in logistics. Inquire about the 3PL’s processes for monitoring and ensuring adherence to these standards. Equally important is understanding their approach to handling instances of non-compliance. A transparent and proactive strategy for addressing deviations is indicative of a 3PL’s commitment to maintaining the highest industry standards.
- Can they provide examples of successful QA initiatives with previous clients?
Case studies offer insights into a 3PL’s practical application of QA principles and their impact on supply chain performance. Real-world examples speak volumes about a 3PL’s ability to translate QA principles into tangible results. Request case studies that highlight specific QA initiatives, their implementation, and the subsequent impact on supply chain efficiency. These examples provide a practical understanding of how the 3PL approaches QA challenges and their track record in delivering successful outcomes for clients.
Collaborative QA Approach
Opting for a 3PL partner that fosters a collaborative QA approach is essential. Communication and collaboration between the client and the 3PL are integral components of successful quality assurance. Your 3PL provider should embrace a collaborative ethos, working closely with clients to align QA processes with their unique requirements. This ensures a tailored, proactive, and continuously improving approach to maintaining the highest quality standards throughout the supply chain.
In selecting a 3PL partner, prioritizing quality assurance not only safeguards the integrity of your supply chain but also positions your business for sustained success in an ever-evolving logistics landscape.
The Hanzo Approach to Quality Assurance
Hanzo Logistics is founded on the principle that quality is not merely a standard but a commitment to consistently exceed expectations. Our commitment to quality permeates every aspect of our service, from the moment goods enter our logistics network to their final destination. This dedication forms the bedrock of our client partnerships, instilling confidence in the reliability of our supply chain solutions.
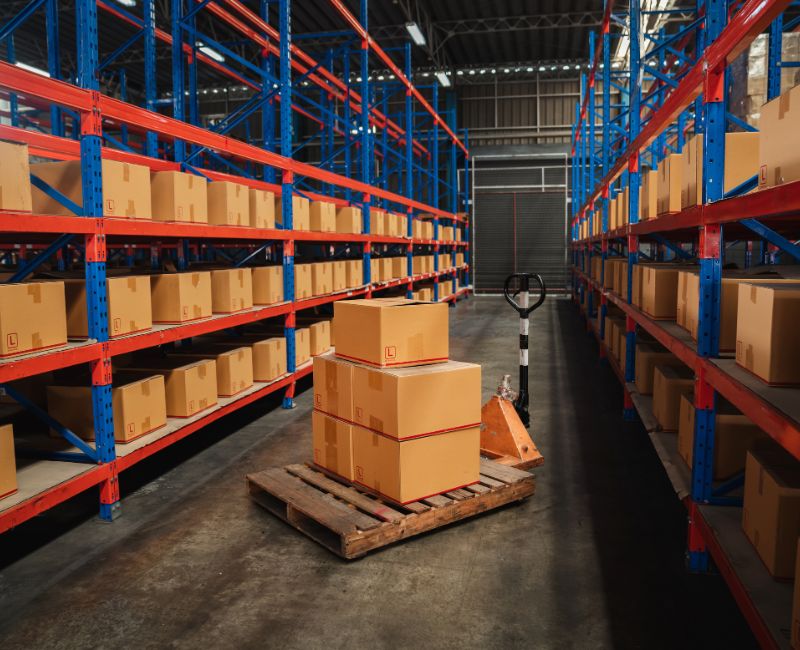
QA Processes and Procedures
Inspection and Testing Protocols: Rigorous inspection and testing protocols lie at the heart of our QA processes. From the meticulous examination of incoming inventory to stringent testing during transportation, we ensure that each product adheres to the highest standards. Our inspection protocols encompass not only product quality but also packaging integrity, ensuring that the entire supply chain is fortified against deviations.
Continuous Improvement Initiatives: In the ever-evolving landscape of logistics, stagnation is not an option. Hanzo Logistics places a premium on continuous improvement initiatives within our QA framework. Regular assessments of processes, feedback loops, and technological integrations allow us to proactively identify areas for enhancement. This commitment to continuous improvement ensures that our QA practices are not only current but also forward-thinking, adapting to industry shifts and client needs.
By adhering to stringent QA processes and fostering a culture of continual improvement, Hanzo Logistics sets the standard for reliability and quality in the logistics industry. Our clients can trust that their supply chain is not just managed but optimized with an unwavering commitment to delivering excellence.
Industry Trends and Best Practices
The dynamics of quality assurance in logistics are continuously shifting in response to changing consumer expectations, regulatory updates, and technological advancements. Companies that stay at the forefront of this evolution can proactively integrate emerging QA strategies, ensuring their operations remain current and effective.
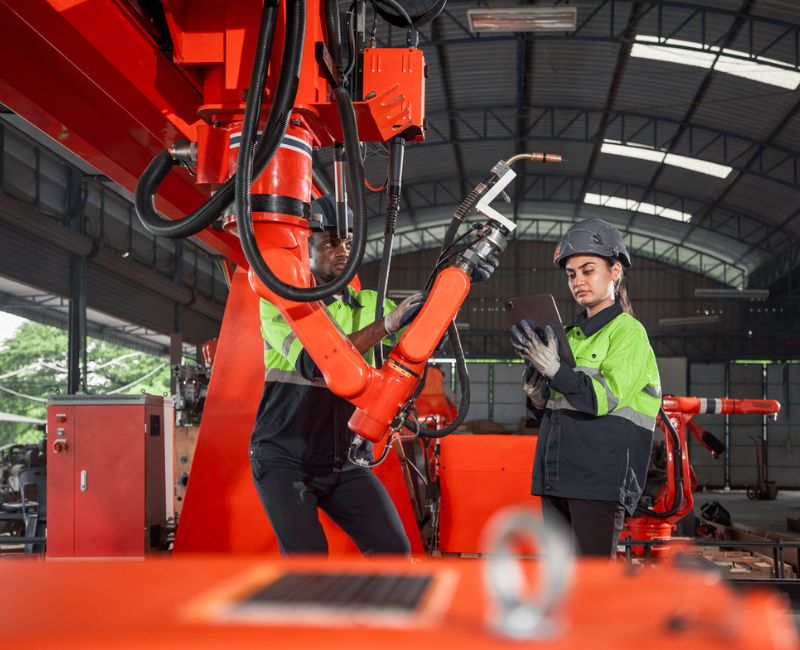
Adopting Industry Best Practices
The pursuit of industry best practices is akin to setting a compass for operational excellence. It involves a diligent examination and integration of methodologies that have proven successful across the logistics landscape. By aligning quality assurance processes with these benchmarks, companies ensure not only the consistency and quality of their services but also the adherence to standards acknowledged and respected within the broader logistics community. Best practices encompass a spectrum of elements, including procedural protocols, compliance measures, and quality benchmarks, collectively contributing to the refinement and optimization of logistics operations.
Technology and Innovation in QA
Technology and innovation are catalysts for transformative change in logistics QA. Leveraging cutting-edge technologies can enhance QA capabilities, from advanced data analytics for predictive quality assessments to the integration of real-time tracking systems. This commitment to innovation not only optimizes efficiency but also ensures that companies benefit from the latest advancements in logistics QA.
Advanced-Data Analytics for Predictive Quality Assessments: Leveraging advanced data analytics empowers companies to conduct predictive quality assessments. This strategic use of data allows for the anticipation of potential issues before they manifest, providing a proactive approach to maintaining high-quality standards throughout the supply chain.
Real-Time Tracking Systems for Enhanced Visibility: The integration of real-time tracking systems enhances visibility across the supply chain. By providing actionable insights, these systems enable swift responses to deviations, ensuring that logistics operations remain agile and responsive to dynamic conditions.
Embracing innovation not only streamlines quality assurance processes but also positions companies at the forefront of the logistics industry. This approach fosters a culture of adaptability and responsiveness to the evolving needs of clients and the market. In essence, the marriage of technology and innovation with QA not only elevates the quality of logistics services but also sets the stage for continuous improvement and future-proofing in a dynamic and competitive landscape.
Upholding Excellence in Business through Quality Assurance
In an era of dynamic market shifts and evolving consumer demands, the importance of quality assurance in logistics extends beyond a singular operational consideration. It stands as a strategic imperative, ensuring not only the delivery of high-quality products and services but also fortifying the resilience of supply chains against unforeseen challenges. The continuous commitment to QA is a timeless investment in the enduring success of logistics operations.
In forging partnerships that prioritize quality assurance, businesses not only enhance their operational efficiency but also position themselves as leaders in an industry that demands unwavering commitment to quality. As the logistics landscape continues to evolve, the principles of QA remain a steadfast guide, ensuring that every link in the supply chain is a testament to excellence and reliability.
At Hanzo Logistics, we encourage businesses to actively embrace QA as a catalyst for sustained growth and client satisfaction. Our commitment to excellence – fortified by robust processes and a collaborative ethos – serves as a testament to the transformative impact of prioritizing quality assurance. Invest in the reliability of your supply chain by exploring how Hanzo Logistics’ comprehensive quality assurance services can elevate your logistics operations.